When Hayree Hashim first started playing sape at 15 years old, he was hooked. Not just by how the instrument sounded but in how it was made.
So much so that 13 years later, he’s running his own full-time brand called SHAPE SAPE (SHAPE) and hand-making sapes from scratch.
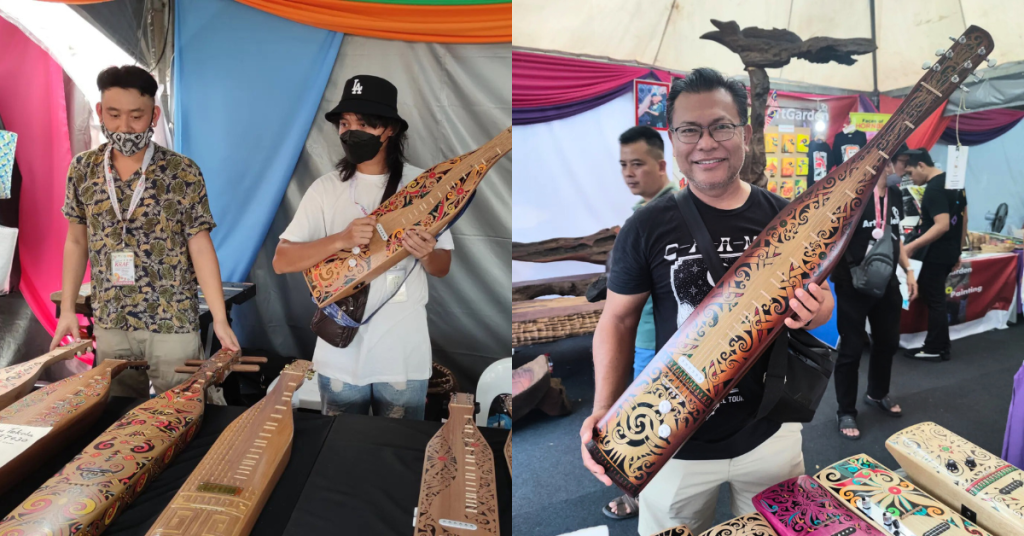
Born out of a love for music
Born and raised in Miri, Sarawak, Hayree shared that sape wasn’t as popular of an instrument back then as it is now. “When I started playing it, it was hard to get your hands on one. You had to go to the Orang Ulu kampung to purchase it,” he said.
The reason was that the sape’s origins can be traced back to the Orang Ulu community in Sarawak.
According to the National Department for Culture and Arts (JKKN), sape is traditionally used by the Kenyah, Kayan, and Kelabit tribes. It used to only be played during medical ceremonies in the longhouse. But it has since gradually become a social tool used as a form of entertainment.
His interest in making the instrument came shortly after getting his first sape. “Then when I was 18, I started to try making it, but it was not so good,” he confided.
A year later, he moved to Kuching and found a sape master named Dines Ngau Wan. “There, I really learnt the proper way to make a sape.”
It was around this time that Hayree began seeing the instrument’s demand growing rapidly. “And yet, the supply was low,” he recalled. “I took that opportunity and felt a great responsibility to keep this instrument alive.”
This led to the establishment of SHAPE in 2017.
He’s a one-man sape workshop
Currently still a home-based business, all of SHAPE’s sapes are handmade from A to Z by Hayree himself.
Like most artists, he starts the process by coming up with a design. The sape’s dimensions are then sketched onto a wooden block, which he later cuts using a chainsaw.
Once the rough body shape of the sape is cut, Hayree hollows out the back using beliung. “[It’s] an old tool used for making boat holes back in the olden days,” he explained. “Once we have the rough body, [an] angle grinder is used to smoothen the surface of the sape.”
Afterwards, a layer of lacquer is sprayed on the sape’s body to treat it before motifs and designs are sketched and drawn on it. He’ll apply another layer of lacquer for extra protection. The final step is putting on the accessories, including the strings, electronic pickup, and machine head.
A total of about two weeks is needed to complete the whole process, so he sets a limit of making a maximum of 10 units a month for quality control.
Despite having six years of experience professionally making the instrument, Hayree finds the most challenging aspect to be mastering the tools used in every step. “It took years for me to master each tool, because these tools require a lot of patience and practice to get used to it.”
“It is dangerous if you can’t handle it correctly. And of course during my process of handling and learning the power tools, I gots cuts and bruises even until now. There is going to be blood involved if you want to be a sape maker on top of sweat and tears,” he quipped.
Trying to keep up with the times
The starting price for SHAPE’s sapes is RM750 for a medium size, and RM1,000 for standard. Some other factors that affect the pricing include the design and specifications.
While the brand carries ready-made stocks, Hayree also welcomes orders for custom-made sapes. Usually, a 20% deposit is required to confirm the order. The balance is to be paid once the sape is ready and delivered.
As for the R&D process, the Sarawakian shared that he’s continuously improving on his work. “If there are any mistakes or deficiencies that should be improved [upon], I will make the improvements,” he stated.
Speaking to Vulcan Post, Hayree shared that the brand’s aim isn’t just to make sape, but to also keep upgrading the instrument, and not just aesthetically.
“I want sape to be recognised as a musical instrument with up-to-date technologies, and not merely a traditional instrument,” he declared.
As such, he adapts certain elements of sape-making from other instruments, like guitars. For example, his R&D found that the procedure and tools used to make guitars can be used to make better quality sape.
“For me, that is the way to keep sape evolving and keep its relevance in the market,” he added.
The instrument is slowly gaining appreciation
Interestingly, Hayree confided that he started the brand with zero capital. The tools he used before were from his family and the wood was sourced himself from the jungle.
In terms of revenue, he said it fluctuates from time to time.
“There were months where I made below RM5K and there were some months that I made up to RM10K. And there was even a month that I made zero sales because sape is not something people buy daily. This is why I think sape-making is not a sustainable career yet,” he said.
That said, he mentioned that demand for sape is growing every day. There was even a point in his career where he couldn’t produce enough of them to meet the demands.
“For us here, now in East Malaysia, sape is a musical instrument legacy that we are proud of. But that’s not the case when I started playing sape when I was a teenager. Not a lot of people cared about it,” he said.
“Gratefully now, sape is well-known and well-appreciated by our people. Parents started to encourage their kids to start playing the sape from a young age and even the older generation started to learn it as well.”
He hopes that over time, this shift in interest could drive higher demand. And eventually, Hayree would like to have a sape-making factory for large scale production. “So that sape can be seen in any musical instrument shop,” he envisioned.
Featured Image Credit: SHAPE SAPE